MISHub QI
Summary Table of Concrete Slump Ranges According to European Standards
Summary Table of Concrete Slump Ranges According to European Standards
Eurocode 2 (EN 1992-1-1) and NP EN 206 establish clear guidelines for the behaviour of concrete under different execution conditions, with emphasis on ease of placement and compaction.
Workability Class (S) |
Slump Interval |
Description and Usage Recommendations |
S1 (Low workability) |
10 to 40 mm |
Low fluidity concrete, suitable for structural elements with simple geometry, where compaction is done manually. Ideal for high-strength concrete. |
S2 (Medium workability) |
50 to 90 mm |
Concrete with good fluidity, suitable for conventional civil construction works, such as floors, beams and pillars. Compaction by mechanical vibration. |
S3 (High workability) |
100 to 150 mm |
Fluid concrete, ideal for elements with complex shapes or requiring greater precision in execution. Used for molding forms on site and more complex works. |
S4 (Very high workability) |
160 to 210 mm |
Highly fluid concrete, used in self-compacting concrete and for easy filling of complex shapes. |
S5 (Extreme workability) |
220 mm and above |
Extremely fluid concrete, suitable for situations such as self-compacting concrete, where movement and filling of forms is essential, including precast concrete. |
Please note: Concrete specification goes far beyond simply checking the slump test on site. Although the table below provides a quick guide to workability classes, it is intended only as a guide to recommended slump ranges and is not a substitute for the detailed analysis and technical expertise required for each specific project.
Why is the Slump Test Not Enough?
Slump is only one of the control parameters in the characterization of concrete, being mainly related to its workability. However, the behavior of concrete in the fresh and hardened state depends on a broader combination of factors, such as:
- Concrete strength class (C20/25, C30/37, etc.);
- Type and granulometry of aggregates used;
- Water content and water/cement ratio (w/c);
- Type and dosage of chemical additives (plasticizers, superplasticizers, retarders, etc.);
- Durability requirements (aggressive environment, exposure to sulfates, etc.);
- Temperature and environmental conditions during transport and application.
For example , a concrete with high slump may appear to have adequate workability, but without an optimized mixture, it may suffer segregation or loss of homogeneity , compromising the strength and durability of the structure.
Consultation and Adaptation to Standards
The table should be understood as a starting point for identifying the workability class appropriate for the type of work, and also serves as a quality control and inspection tool, ensuring that the concrete used meets the technical specifications and performance requirements required for the execution of the work. For complete specifications, it is essential to consult applicable technical standards, such as standard NP EN 206-1:2007 “Concrete – Part 1: Specification, performance, production and compliance” , which defines the composition, production and compliance requirements for concrete.
Consult the Guide for using the NP EN 206-1 standard here.
Furthermore, the correct selection of concrete properties must often be carried out in collaboration with:
- Experts in the field of civil engineering or concrete technology;
- Representatives of the ready-mix concrete plant , who can adjust the mix to the specific conditions of the project.
Decisions about which concrete to use should not be made in isolation or based solely on a simplified table. Detailed analysis and specialist technical support are essential to ensure the safety, durability and quality of the structure.
Author: Eng. Francisco Quisele Jr.
Date of publication : 01/09/25
Share
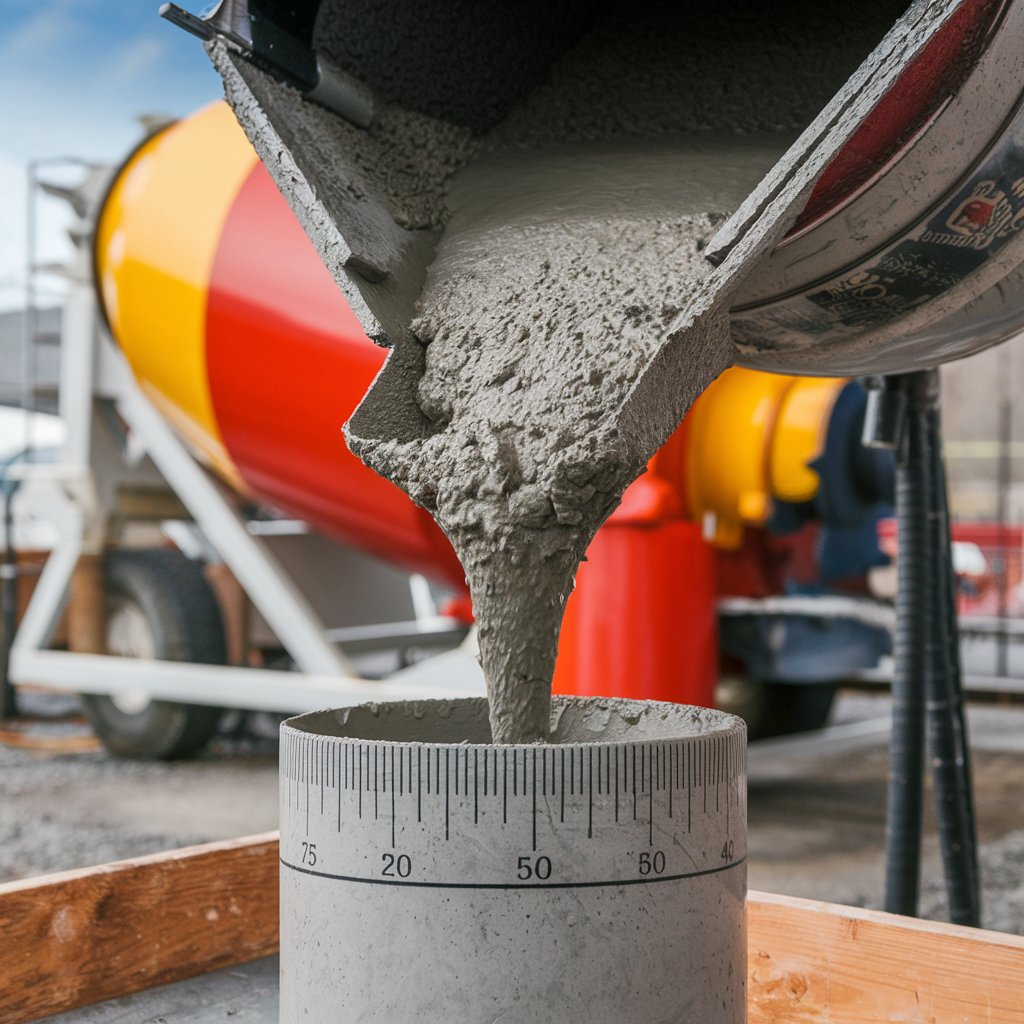